2025 Manufacturing Survival Guide: These 5 Trends Will Determine the Fate of Enterprises
Release time:
2025-02-20
When Tesla's humanoid robot walks into the workshop, agilely assisting workers in completing complex tasks; when CATL's zero-carbon factory secures EU orders with its green advantage and shines in the international market, are you still competing on price with overseas giants using traditional equipment? In 2024, as new energy vehicles continue to expand production, the EU carbon tariff takes effect, and DeepSeek sparks an industrial AI revolution,the manufacturing industry is undergoing unprecedented waves of change. Facing these industry trends, if companies want to survive and develop in 2025 and beyond, they must keep up with the following 5 major trends.
When Tesla's humanoid robot walks into the workshop, agilely assisting workers in completing complex tasks; when CATL's zero-carbon factory secures EU orders with its green advantage and shines in the international market,
are you still competing on price with overseas giants using traditional equipment? In 2024, as new energy vehicles continue to expand production, the EU carbon tariff takes effect, and DeepSeek sparks an industrial AI revolution,
the manufacturing industry is undergoing unprecedented waves of change. Facing these industry trends, if companies want to survive and develop in 2025 and beyond, they must keep up with the following 5 major trends.
From "machine replacing humans" to "system replacing brain"
Today, the density of industrial robots in China's manufacturing sector has surpassed 380 units per 10,000 people (2023 data), a figure that vividly demonstrates the achievements of "machine replacing humans." An increasing
number of companies are introducing industrial robots to improve production efficiency and reduce labor costs. However, the development of smart manufacturing goes beyond this, advancing into the "system replacing brain"
phase. Predictive maintenance is a key manifestation of this. Sany Heavy Industry collects real-time operational data from equipment using IoT devices and, through big data analysis and algorithms, can provide precise early
warnings of potential failures. This initiative directly reduced maintenance costs by 40%, significantly reducing downtime losses caused by unexpected equipment failures and ensuring continuous production.
Flexible production lines are also a highlight of smart manufacturing. The Haiercaos platform is very powerful and supports switching product models within 10 minutes. In today's increasingly diverse market environment,
companies can quickly adjust production to meet different order needs, which means seizing market opportunities and improving customer satisfaction and corporate competitiveness.
Carbon footprint becomes a new entry ticket
The implementation of the EU carbon tariff acts like a sword hanging over exporters, forcing companies to undergo green transformations. Products exported to the EU require companies to pay a tariff of 30 - 50 euros per ton of CO₂. For traditional
high-energy-consuming manufacturing industries, this undoubtedly represents significant cost pressure, but it is also an opportunity to promote green development. Contemporary Amperex Technology Co. Limited (CATL) sets a good example in
green transformation; its German factory achieves 100% green electricity supply. This not only reduces carbon emissions and meets the EU’s stringent environmental standards but also enhances the company's image and competitiveness in the
international market.
Data-driven "second production line"
Industrial Internet is becoming a new engine for the development of manufacturing, and Midea Group's M.IoT platform is a typical representative. This platform connects more than 100,000 devices, and by deeply mining and analyzing the operation data
of the equipment, it optimizes production processes, increasing the yield rate by 15%. This means higher product quality, lower defect rates, reduced production costs, and enhanced market competitiveness of the products.
Digital twin technology is making significant strides in the industrial internet. Aerospace companies use digital twins for virtual debugging, which allows them to simulate product performance under various complex conditions in advance, promptly identify
design flaws, and optimize them. This technology directly reduces the R&D cycle by 70%, enabling companies to bring products to market faster and seize industry leadership
From "Going Out" to "Localization"
In recent years, there has been a surge in factory construction in Southeast Asia, with foreign investment in Vietnam's manufacturing sector growing by 48% in 2023. An increasing number of companies are choosing to set up factories in places like Southeast Asia,
taking advantage of lower labor costs, preferential policies, and access to large markets, thereby reducing production costs, getting closer to target markets, and minimizing the impact of trade barriers.
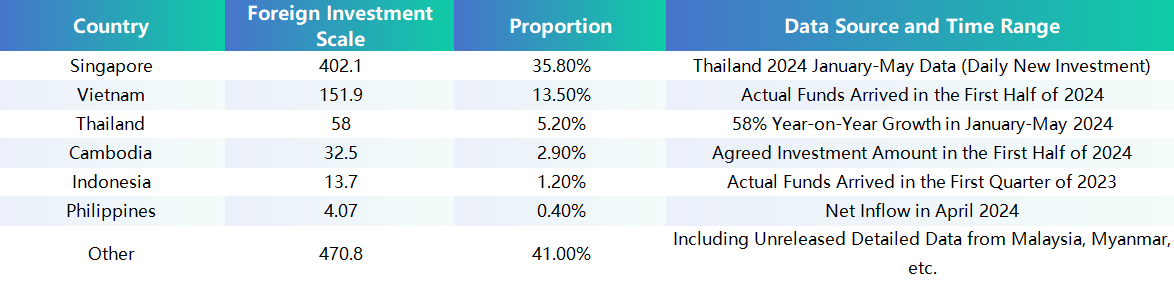
Fuyao Glass has established a unique supply chain system in the process of globalization. It has built a "mine - factory - customer" vertical system in the United States, achieving full industrial chain localization from raw material extraction, manufacturing to sales.
This not only ensures stable raw material supply but also enhances market response speed,strengthening the company's competitiveness and risk resistance in overseas markets.
Compound engineers become scarce resources.
According to the prediction of MIIT, the talent gap in smart manufacturing will reach 3 million in 2024. As manufacturing transitions towards intelligence and digitalization, there is a surge in demand for composite engineers who understand both technology and management,
are familiar with traditional manufacturing processes, and master cutting-edge technologies. However, the supply of such talents is far from meeting corporate needs, and talent shortage has become a key factor constraining corporate development. Siemens's "dual system"
model of school-enterprise cooperation provides a solution to the talent issue. Under this model, students learn theoretical knowledge at school while gaining practical experience in enterprises. After graduation, they can quickly adapt to job requirements and provide a large
number of high-quality composite talents to enterprises. Manufacturing enterprises that wish to stand out in future development must prioritize talent cultivation and recruitment, exploring talent strategies suitable for themselves.
📈 Facing changes, Constant Storage Machinery provides a one-stop solution for intelligent workshop transformation:
√ 20 years of industry know-how accumulation
√ Jointly developed an intelligent control system with several leading companies in the industry.
√ Successfully assisted 300+ enterprises in their overseas expansion strategies.
Latest News